Purpose-built environmental data solutions for complex manufacturing operations
Manufacturers face a uniquely complex set of challenges when it comes to environmental data - from fragmented systems and operational silos to shifting baselines and audit pressures.
Facts about manufacturing firms and your environmental data:
Your operations are complex and always changing
Track your data at any level of your organization – and keep up with change
Your structure is always shifting - products evolve, sites expand, ownership changes. Minimum helps you model your inventory and track emissions in a way that reflects the true shape of your business. Explore Minimum’s step-by-step features that will help you achieve accurate and time-sensitive data wherever you are in the manufacturing value chain.
You are a multi-layered organisation with a constantly shifting baseline
- Dispersed operations and complex ownership: you operate across multiple sites, jurisdictions and ownership structures (e.g. subsidiaries, joint ventures), resulting in complex organisational boundaries.
- Change is the only constant: you have shifting product lines, evolving supply chains and ongoing M&A activity. Your baseline is constantly changing, making it hard to track and achieve consistency in your inventory.
- Low data visibility: your data lives in silos – from ERP systems to site-level spreadsheets to energy meters – which makes capturing all the nuance of your data extremely challenging.
Minimum’s purpose-built solutions
- Model your business hierarchy in multiple ways: Reflect your manufacturing footprint across legal entities, production sites, and operational structures – whether grouped by facility, region, product line, or reporting entity.
- Time travel to see your historical inventory: Seamlessly track how changes in plant structure, acquisitions, or production activity impact your carbon data – even across multi-year baselines.
- Capture every detail of your business: Map every nuance of your firm and the associated data owners and stakeholders. Whether it’s joint ventures, business units sharing a single facility, multiple sub-meters in a single site.
You sit on huge volumes of data but it’s rarely in one place or the right format
- Data is scattered across systems, teams and supply chains: your data is often locked in siloed systems, spread across different business units, facilities, and external partners – making it hard to access, let alone ingest.
- Inconsistent formats and file types: from IoT data to equipment logs, purchase invoices, and maintenance reports – your data doesn’t arrive clean or standardised, and almost none of it is structured for emissions calculation.
- Manual data processing eats up time and resources: collecting, transforming, and stitching together this data is often a manual, repetitive process – prone to delays, errors, and bottlenecks.
Minimum’s purpose-built solutions
- Gather data from inside & outside your organisation: collect relevant data from where it lives – MES, ERP, energy meters, and supplier portals – regardless of where or how it’s generated.
- Unify disparate sources of data: Ingest everything from PDFs and CSV files to machine-level logs and site spreadsheets — and bring them into a structured source of truth. No manipulation required on your side.
- Effortlessly cleanse inputs: automatically validate and transform messy, site-level data into structured, calculation-ready inputs with built-in logic for manufacturing formats.
You create value through differentiated production processes, which generate unique footprints
- Scope 1: your direct emissions from on-site fuel combustion, process emissions, and fugitive gases are material, and require bespoke treatment using industry-specific methodologies.
- Scope 2: you have significant electricity demand, plus heat and steam use, across global locations. You often need to match demand with renewable energy purchases or certificates.
- Scope 3: you have deep, multi-tier supply chains with limited visibility of data availability and quality. You may have a substantial logistics footprint, as well as downstream processing, use phase and end of life emissions.
Minimum’s purpose-built solutions
- Utilise our extensive, always updated Emissions Factor library: get immediate access to verified factors tailored to manufacturing – including fuels, feedstocks and energy types – across multiple geographies.
- Encode business-specific methodologies: configure emissions calculations to reflect your unique production methods, use cases, and operational complexities.
- Apply GHG Protocol compliant methodologies across Scope 1, Scope 2, and Scope 3: cover every relevant emissions source with confidence, from direct combustion to purchased electricity and supply chains.
You rely on high resolution real-time data to optimise operational decision making
- High-frequency data for operational feedback: you need to monitor emissions, energy use, and process efficiency in near real-time – to flag and monitor decarbonisation opportunities on the factory floor.
- Process-relevant KPIs and intensity metrics: from emissions per unit produced to energy use per operating hour, your performance depends on tracking metrics grounded in how manufacturing inputs and outputs actually flow.
- Granular tracking across sites, assets, and org levels: to stay on target, you need to disaggregate data by site, asset, or business unit — while also rolling it up to track organisation-wide goals.
Minimum’s purpose-built solutions
- Use granular, high-quality, high-frequency data to analyse and improve your business’ environmental performance: Minimum’s platform creates detailed data archive and is poised to identify decarbonisation opportunities and confidently identify effective levers of change.
- Easily implement the intensity metrics which make sense for your business model: Configure emissions per tonne of output, per production hour, or per revenue for example – whatever aligns to how your factory runs.
- Track group-level, entity-level, division-level targets & progress with ease: monitor environmental performance across your corporate structure – from HQ to regional divisions to individual plants – ensuring accountability and alignment.
You make data-driven decisions based on variables from multiple systems
- Disconnected systems across production and enterprise layers: your data lives across ERPs, MES, EMS, logistics platforms, and cloud tools – environmental data isn’t integrated or easily accessed alongside operational metrics.
- Environmental data needs to move at the pace of production: your environmental data is not being ingested at high enough frequency to sync with other business critical variables like output, up-time, or throughput.
- Limited visibility across business functions: your environmental data needs to be shareable with teams outside sustainability — from procurement to finance to operations — for them to act on and include in decision-making.
Minimum’s purpose-built solutions
- Integrate with other systems by using our input API: Seamlessly pull environmental data from your ERP, MES, EMS, or logistics tools — reducing duplication and manual effort for site teams.
- Ingest data programmatically at a suitable cadence: Configure data ingestion according to the specific frequency your organisation requires, allowing automation without disruption.
- Feed rich carbon and environmental data into other systems using our output API: Export validated metrics into PowerBI, Tableau, or internal dashboards used by ops, procurement, or finance teams.
Collaboratively transform fragmented data into clean, automated insights that are audit-ready
Footprint calculations are only as good as the data behind them - and in automotive, that data can be messy. Minimum's platform automates the heavy lifting, providing you seamless collaboration and control over the process so that you can trust every number and explain every figure.
Explore Minimum’s cross-cutting features below that will underpin your carbon journey.
Your footprints are hard to audit – with scattered data and complex calculations across the value chain
- Unclear data lineage across fragmented systems: your activity data sits in different formats across MES, EMS, spreadsheets, and emails — making it hard to trace how figures were derived, or which assumptions were used.
- Industry-specific methods and opaque calculations: your footprints often rely on complex, sector-specific methodologies with layered estimates and limited visibility.
- Audits drain time and resources: reconstructing a full picture from disjointed systems takes you weeks — pulling in finance, operations, and sustainability teams to piece together what should already be visible.
Minimum’s purpose-built solutions
- Explain every data point with complete end-to-end transparency on the full data flow: Every data point in the Minimum platform is accompanied by a complete audit log, providing total transparency over every step of the process from cleansing, validation, calculation, and consolidation.
- Unify activity data into a single set of records for analysis: Consolidate varied inputs (from different production lines, facilities, or suppliers) into a clean, traceable dataset for audit or reporting.
Your environmental governance is complex — with many users, moving parts, and compliance needs
- Multiple user roles across plants, business units, and functions: you have many internal stakeholders — from site-level data submitters to sustainability, finance & ops teams – each needing different access levels and responsibility.
- Manual workflows create risk and inefficiency: your processes often rely on spreadsheets, emails, and manual reviews to consolidate inputs, check for errors, and sign off on data — introducing delays and avoidable mistakes.
- Overlapping compliance and documentation requirements: you operate across multiple jurisdictions, each with its own reporting expectations, requiring evidence collection and audit-ready documentation at scale.
Minimum’s purpose-built solutions
- Access controls: assign permissions based on role — whether it’s a plant-level submitter, division controller, or group sustainability lead — so contributors only see what’s relevant to them.
- Configurable approval workflows & variance checks: activate maker-checker workflows and automated flags to catch issues — ideal for high-volume, multi-facility reporting environments.
- Upload evidence & documentation: all data is attached to the audit trail. Capture and store compliance-relevant documents (like RECs, invoices, or certificates) alongside the data — ready for audit or regulatory submission.
You face complex coordination challenges when managing environmental data collection at scale
- High volume of contributors across global operations: you depend on timely input from dozens — sometimes hundreds — of contributors, spread across production sites, departments, and regions.
- Manual follow-ups slows progress and drains resources: chasing submitters through emails, spreadsheets, or shared folders makes it difficult to know who’s behind, what’s missing, and what’s blocking progress.
- Lack of real-time visibility creates blind spots: you struggle to see progress by site, contributor, or business unit — making it hard to intervene early, resolve issues, or meet internal timelines and reporting deadlines.
Minimum’s purpose-built solutions
- Monitor progress of data submission from systems & people across your business: Get real-time visibility into who’s submitted what — broken down by region, site, team, or individual contributor.
- See live progress by region, business unit, individual, and more: Access real-time progress dashboards broken down by geography, departments, and individual data owners, making it easier to manage your environmental data collection across complex organisations.
- Send reminders & interact with data submitters inside the platform: Communicate seamlessly within the platform to prompt late responders, request clarification, or provide direct support, reducing delays and increasing accuracy.
You rely on a wide and varied network of internal and external data submitters
- Dispersed data owners: from facility managers to procurement teams to suppliers, data lives across business functions, subsidiaries, and third-party partners – each with different systems and levels of sustainability expertise.
- No standard process for how or where to submit data: without a centralised, structured submission workflow, data gets lost in inboxes or uploaded in inconsistent formats – slowing down progress and increasing errors.
- Limited supplier visibility beyond Tier 1: deep supply chains often lack maturity in carbon data tracking, with minimal access to reliable Scope 3 data from upstream suppliers and vendors.
Minimum’s purpose-built solutions
- Dead simple data submission: easily collect data across your organisation with a straightforward submission portal, designed for clarity so even non-technical or non-specialist staff can contribute data with confidence.
- Collaborate through submissions in-platform: assign tasks, send nudges, and track submission status — all without relying on emails, spreadsheets or offline reminders.
- Collect Scope 3 data directly from 3rd parties such as suppliers and investments: enable suppliers to submit emissions activity through a dedicated portal – making value chain engagement structured and scalable.
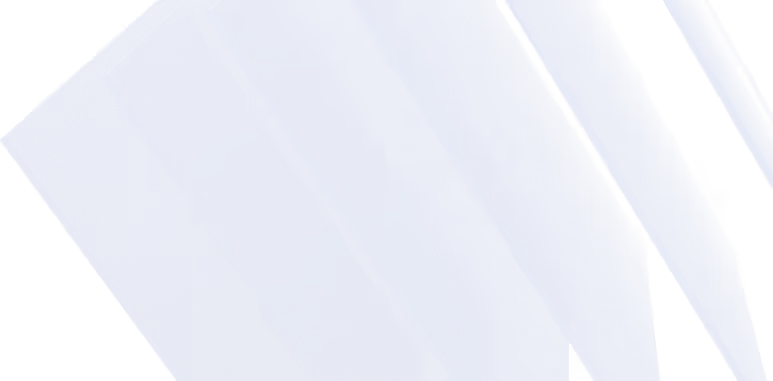